
Introduction: Polyaspartic flooring has gained popularity in recent years as a durable and versatile flooring solution for both residential and commercial spaces. This advanced coating technology offers a range of benefits, including fast curing times, exceptional durability, chemical resistance, and aesthetic appeal. In this article, we will take a closer look at the polyaspartic flooring process, exploring its application, advantages, and considerations.

- Understanding Polyaspartic Flooring: Polyaspartic coatings are a type of aliphatic polyurea coating that provide a high-performance protective layer for concrete floors. They are known for their quick curing times, allowing for faster installation and reduced downtime. Polyaspartic coatings can be clear or tinted and are available in a variety of finishes, including glossy, satin, or matte.
- Surface Preparation: Like any flooring system, proper surface preparation is crucial for a successful polyaspartic flooring installation. The concrete substrate must be clean, dry, and free of any contaminants such as oil, grease, or existing coatings. Surface preparation methods may include shot blasting, diamond grinding, or acid etching to ensure proper adhesion.
- Priming and Base Coat Application: Before applying the polyaspartic coating, a primer is typically used to enhance adhesion and penetration into the concrete substrate. The primer is applied using a roller or spray equipment and allowed to cure according to the manufacturer’s instructions. Once the primer is dry, a base coat of polyaspartic material is applied evenly to the floor using a roller or squeegee.
- Decorative Options: Polyaspartic flooring offers various decorative options to enhance the appearance of the floor. These options include color flakes, metallic pigments, quartz aggregates, or custom designs. Color flakes are a popular choice as they add texture, hide imperfections, and provide a vibrant, multi-dimensional look to the floor. Metallic pigments create a unique, shimmering effect, while quartz aggregates offer a durable and slip-resistant surface.
- Top Coat Application: After the base coat and decorative elements have been applied, a clear polyaspartic top coat is applied to provide additional protection and a glossy finish. The top coat enhances the durability, chemical resistance, and UV stability of the floor. It is crucial to follow the manufacturer’s instructions regarding the recommended number of top coats and curing times between each coat.
- Fast Curing Times and Minimal Downtime: One of the significant advantages of polyaspartic flooring is its fast curing times. Unlike traditional epoxy coatings that may take several days to cure, polyaspartic coatings can cure within a few hours. This rapid curing allows for a shorter installation process, reduced downtime, and faster return to service for the space.
- Maintenance and Longevity: Polyaspartic floors are relatively low-maintenance, making them ideal for high-traffic areas. Regular cleaning with mild detergents and occasional buffing or polishing can keep the floor looking its best. When properly maintained, polyaspartic flooring can last for many years, withstanding heavy foot traffic, impacts, and chemical spills.
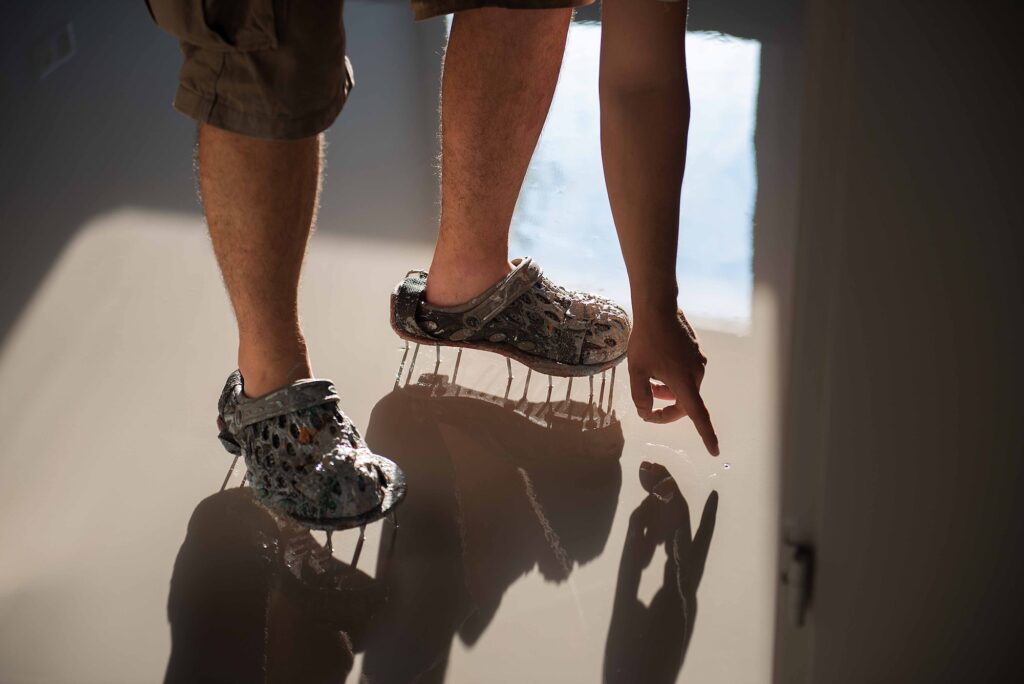
Conclusion: Polyaspartic flooring offers a superior solution for those seeking a durable, visually appealing, and fast-curing flooring option. With its advanced coating technology, the polyaspartic flooring process delivers exceptional performance and aesthetic versatility. By following proper surface preparation, application techniques, and maintenance guidelines, you can enjoy the benefits of a long-lasting and beautiful polyaspartic floor in your residential or commercial space.
- Best Pills for Erection: Your Comprehensive Guide to Enhanced Performance
- TOP 6 Epoxy Resin Applications in 3C Electronics Industry
- The Role of Epoxy Resin in Enhancing Electronics: Applications and Benefits
- A Comprehensive Guide to Epoxy Potting in Industrial Applications
- Essential Tools for Successful Epoxy Resin Flooring Installation