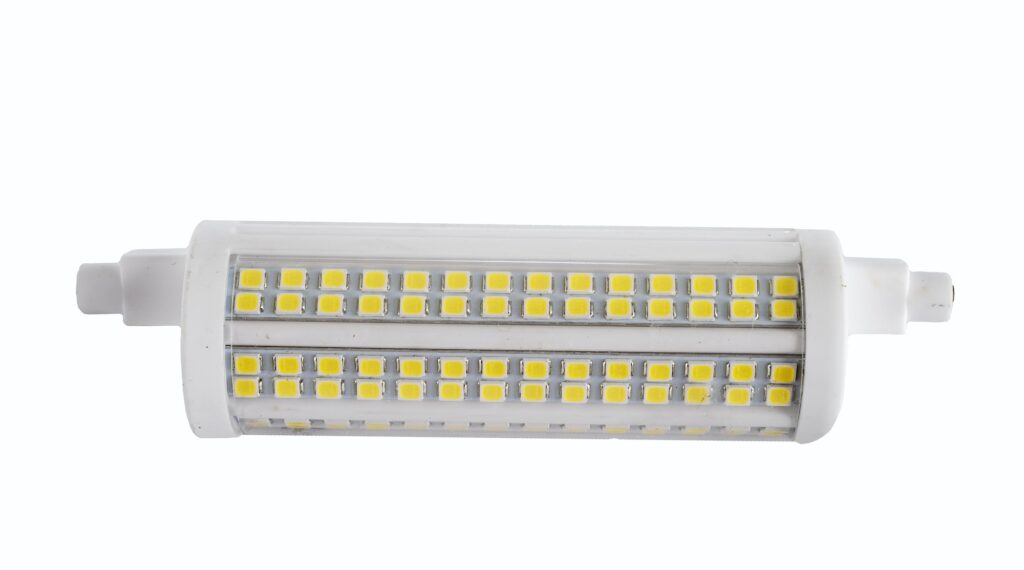
Epoxy potting, a process of encapsulating electronic components or devices in epoxy resin, has become a staple in various industrial applications. Its ability to offer protection, insulation, and stability makes it an invaluable technique across industries such as electronics, aerospace, automotive, and more. In this guide, we’ll delve into the intricacies of epoxy potting in industrial settings, exploring its benefits, methods, and best practices.
Understanding Epoxy Potting: Protection Beyond the Surface
Epoxy potting involves immersing sensitive components or devices, such as circuit boards, sensors, or connectors, into a specially formulated epoxy resin. This encapsulation not only shields the components from external factors like moisture, chemicals, and physical stress but also enhances their durability, reliability, and overall performance.

Benefits of Epoxy Potting in Industrial Applications
- Environmental Protection: Epoxy potting creates a hermetic seal that safeguards electronics from harsh environments, including temperature variations, humidity, and chemical exposure.
- Vibration and Shock Resistance: The epoxy resin’s adhesive properties ensure that components remain securely in place, even in applications subjected to vibrations and shocks.
- Insulation and Dielectric Strength: Epoxy potting provides excellent insulation, reducing the risk of short circuits and enhancing the dielectric strength of components.
- Enhanced Thermal Management: Some epoxy formulations offer excellent thermal conductivity, dissipating heat and preventing thermal stress on sensitive components.
- Corrosion Prevention: Epoxy’s protective layer prevents corrosive substances from reaching the components, prolonging their lifespan.
Epoxy Potting Methods
- Manual Potting: Suitable for small-scale applications, manual potting involves carefully pouring or injecting epoxy resin around components. It offers precision but may be time-consuming.
- Vacuum Potting: This method involves placing components in a vacuum chamber and filling it with epoxy. The vacuum removes air bubbles, ensuring complete encapsulation.
- Pressure Potting: Components are placed in a pressure chamber, and epoxy is injected under pressure. This method reduces the risk of voids or air entrapment.
- Machine dispensing: This method uses a metering mixing and dispensing system for precise and mass production, is the cutting-edge technique of modern manufacturing process widely used in all kinds of product manufacture,the refer machines you can visite ZCX.

Best Practices for Epoxy Potting
- Material Selection: Choose epoxy formulations that match the application’s requirements, such as thermal conductivity, chemical resistance, and flexibility.
- Surface Preparation: Ensure components are clean, dry, and free from contaminants to ensure optimal adhesion.
- Potting Depth and Volume: Determine the appropriate potting depth and volume to provide sufficient protection without excess waste.
- Curing and Drying: Follow the epoxy manufacturer’s guidelines for curing time and temperature to ensure complete resin hardening.
- Quality Control: Inspect potting for uniform coverage, absence of air bubbles, and proper adhesion. Conduct tests for dielectric strength and thermal performance.
- Safety Measures: Wear appropriate personal protective equipment (PPE) and work in a well-ventilated area when handling epoxy resins.
In conclusion, epoxy potting is a vital technique in industrial applications, offering unparalleled protection and performance enhancement for sensitive electronic components. By understanding its benefits, methods, and best practices, industrial professionals can harness the full potential of epoxy potting to ensure the longevity and reliability of their devices in demanding environments.
- Best Pills for Erection: Your Comprehensive Guide to Enhanced Performance
- TOP 6 Epoxy Resin Applications in 3C Electronics Industry
- The Role of Epoxy Resin in Enhancing Electronics: Applications and Benefits
- A Comprehensive Guide to Epoxy Potting in Industrial Applications
- Essential Tools for Successful Epoxy Resin Flooring Installation