BZ-618-18A/B
Features
Characteristics
BZ-618-18A/B is a two-component room temperature curing 100% solid polyurethane resin system, that does not contain any solvents, after curing to form a clear, transparent, crystal clear protective coating, widely used in signs, nameplates, and other crafts drip. BZ-319A/B has excellent weathering and UV resistance after curing, in outdoor sunlight can ensure more than 1-2 years without changing The surface is smooth and transparent, which can enhance the texture of the products and win you the reputation of customers.

Feature Description
BZ-618-18A is a polyisocyanate component, and BZ-618-18B is a polyol component, according to the requirements of different customers can provide different curing material hardness, different curing time, different viscosity products, to meet the requirements of manual drip and mechanical drip.
Composition.
- BZ-618-18A
- 1. Alicyclic isocyanate R-N=C=O
- 2. Polyol resin R-[O-CH2-CH]nOH
- BZ-618-18B
- 1. polyol resin R-[O-CH2-CH]nOH
- 2. alicyclic isocyanate R-N=C=O
- 3. Catalyst C8H8HgO2; CH3COOC6H5Hg
- Color:
- BZ-618-18A: Transparent liquid
- BZ-618-18B: Transparent liquid

Mixing ratio: weight ratio A: B=100:100, the proportioning error is within 2%; and agent A is as accurate as possible
Viscosity value (25℃):
- BZ-618-18A: Curing agent 1100±400 mPa-s
- BZ-618-18B:Main agent 300±100 mPa-s
- After mixing 600±200 mPa-s
- Density (25℃): BZ-618-18A: 1.01±0.05 g/cm3
- BZ-618-18B: 1.01±0.05g/cm3
Operation time (100g, 25℃) 24±5min, recommended being used up within 24min.
Curing time: 25 ℃, 5-6 hours, the temperature decreases, the curing time will increase accordingly; if you need to heat curing, the recommended temperature is 60 ℃, 1 hour to complete curing.
Storage life: In the original sealed barrel, it can be kept for 3 months in a dry environment within the temperature range of 15℃ to 25℃.

Performance after curing: Unit or test condition
- Appearance Transparent and smooth surface without ripple Visual inspection
- Hardness 55±5 Shore -A
- Absorbency ≤0.2% After 30 days of soaking
- Temperature resistance -20℃~80℃
- Weather fastness 24-48 hours artificial climate aging test, Irradiation(340nm)0.5w/m2
- glue color does not change yellow, Relative Humidity:60~80)%
- no oil on the surface, Black panel temperature(65±2)℃
- no pulverization Rainy cycle:18min/102min(spraying time/not spraying time)

Brief introduction of the application process
BZ-618-18A/B has a manual drip type and a mechanical drip type. The manual drip type can be used for a long time and cured slowly, while the mechanical drip type can be used for a short time and cured quickly.
Manual drip process
A.Control the temperature at 25 ℃ and relative humidity <70 %, BZ-618-18A/B Crystallization may occur at low temperature, please heat it at 60 ℃ for 12 hours and then use it again. In winter, the heating time should be extended as far as possible according to the situation.
B. Place the substrate on a horizontal surface and fix it with a self-adhesive.
C. Clean the dust and oil stains on the surface of the substrate.
D. Weighing correctly BZ-618-18A, and BZ-618-18B, mix well according to the weight ratio of 1:1
E. Manual drip injection of the surface of the base material.
F. Use a needle to move the glue to spread over the surface, and remove the residual bubbles.
G.The curing can be completed in 7-9 hours and can be collected for packing. When the temperature is low, the curing time will be longer.

Mechanical drip process
Note: when the automatic glue dropping machine needs to be cleaned, it can be cleaned with ethyl acetate solvent.
- Pour BZ-618-18A and BZ-618-18B into the A B glue barrel of the automatic glue dispensing machine separately. And extract the vacuum for 30 minutes.
- Insert the pump and seal it.
- Adjust the ratio of A and B materials (100:100) with an electronic scale (accuracy 0.1g), place the substrate on the horizontal surface, and fix it with self-adhesive
- Place the bottom material on the horizontal surface and fix it with adhesive.
- Clean the dust and oil on the surface of the substrate.
- Clean the mixing tube and dispensing head with ethyl acetate.
- Stir the glue with a needle to make it spread all over the surface and remove the residual bubbles. When the glue has a wire drawing, put it into the oven at 55-60 ℃ and bake it for 60-90 minutes.
- When the temperature is low, the curing time will be longer.

Operation details and attention (take the manual usage as an example):
Suggested operating environment:
Dry constant temperature dust-free workshop (Recommended workshop operating temperature is 20 ℃ º C~25 º C), ventilated, the humidity in the workshop should be controlled below 70%, and indoor conditions are fixed. Pay close attention to humidity control in the rainy season.
II. Preparation for use:
1) Deal with the substrate to be clean, dry, and free of impurities. If it is a led substrate, it is recommended to wash the solder joint to avoid the reaction between residual components of soldering aid and PU glue. After washing the board, pay attention to wiping the washing part with a dry cloth after the washing water evaporates.
2) Prepare the mixing bottle or dropping bottle and blender. Requirements: clean, dry, and free of impurities. Do not use the mixing bottle or dropping bottle or blender that has been mixed with other glue before. Should pay attention to this.
- Correct weighing BZ-618-18A/B, by weight 1:1. After mixing the glue, please cover and tighten the lid of the glue bottle immediately to avoid steam in the air entering the glue bottle.
III. Stir evenly: Stir evenly in the same direction. Pay attention to scraping the bottom and side wall as much as possible, so that the mixing is more evenly. Stirring time control in 90 to 120 seconds (1 minute and a half to 2 minutes) is enough.

IV. Vacuuming.
Vacuum the mixed glue directly and immediately with a vacuum machine for 90 to 120 seconds (1 minute and a half to 2 minutes) or less.
V. Dispensing
Drop glue onto the surface of the substrate manually, and stir the glue with a needle to make the glue cover the surface. If there are residual bubbles, the needle can also be used to remove them.
It is suggested to use up the prepared glue within 24 minutes to achieve the best effect, and also improve the production efficiency. The fluidity will be affected after more than 24 minutes, which is not conducive to operate
VI. Curing
Natural curing in 12-24 hours. When the temperature is low, the curing time will be longer.
If heating curing is required, the recommended temperature is 60 ℃. The curing time is 60min.
Attention to use and storage of PU glue
On crystallization at low temperature
For BZ-618-18A/B, under 15 ℃ (24-hour average temperature), crystallization may occur after placing more than 24 hours. If the temperature rises, the crystallization phenomenon will disappear.
In autumn or winter, you can recover A glue at 60℃ for 12 hours to clarify the liquid, then take it out and leave it for 30 to 50 minutes to cool slightly before use. (Note, you don’t need to bake the freshly produced glue for so long, but the glue needs to be heated to recover if it is left for too long)

- About Allergy
I. Manual operation of BZ-618-18A/B may be allergic to certain people, such as those who are allergic to chemicals.
II. It’s better to wear film gloves during the operation. Wash hands with soap immediately after an operation and clean the parts in contact with the glue.
III. The glue operation workshop should keep proper ventilation, which can increase the ventilation by the blower.
IV. Prohibited asthma patients.
3) About glue storage and usage
I. The optimum conditions: constant temperature and humidity, 25 ℃ and humidity is below 70%.
II. Recommended environment: in a general workshop environment, it can be stored for three months in a sealed and dark place.
III. The glue should be used up within one month when it has been opened, and the lid should be covered.
IV. In the rainy season, the operation workshop should pay special attention to the humidity. If the humidity is more than 90%, dehumidification is recommended.

4) Curing
I. In constant temperature 25 ℃, 15-24 hours natural curing.
II. If the temperature is lower than 15 ℃ and the temperature difference between day and night is large, it takes 12 to 24 hours to cure.
III. Curing at 60 ℃ for 60min; When the temperature is low, the heating time can be slightly extended.
IV. When the temperature is too low in winter, the workshop can increase the air heater to shorten the curing time.
Package specification
Packing is 5kg, 20kg, 200kh metal barrel
- Storage, transportation, and other precautions
- This product is non-dangerous goods and is transported as general chemicals.
- Please store under the condition of 15 ℃ – 25 ℃ relative humidity < 70% and keep away from light. Please refer to the packaging barrel for the storage period of the product.
- When the material is in contact with the eyes, immediately open the eyelid and wash with plenty of water for more than 15 minutes.
- When the material comes into contact with the skin, wipe it off with a cloth and wash the affected part with water and soap.
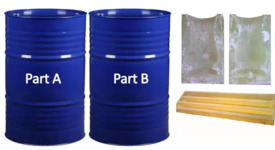
*Note: the above performance data shows that the humidity of the product is below 70% and the temperature is 25℃ ±3 ℃. The test data is only for customers’ reference, and can not guarantee all the data that can be achieved in a specific environment. Please subject to the measured data.
- Best Pills for Erection: Your Comprehensive Guide to Enhanced Performance
- TOP 6 Epoxy Resin Applications in 3C Electronics Industry
- The Role of Epoxy Resin in Enhancing Electronics: Applications and Benefits
- A Comprehensive Guide to Epoxy Potting in Industrial Applications
- Essential Tools for Successful Epoxy Resin Flooring Installation